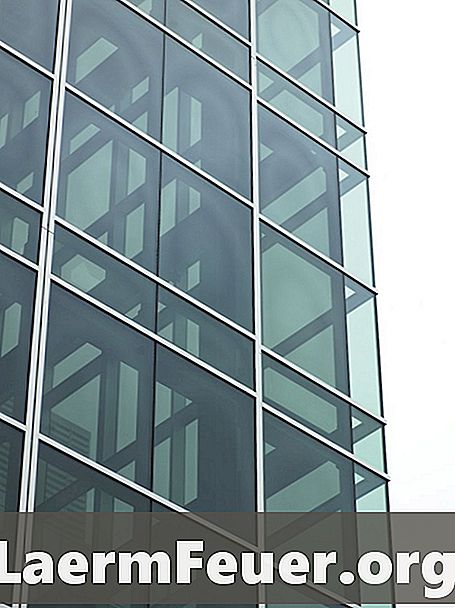
Innehåll
Säkerhetsglas, innan det används i hem, civilbyggnad och inom transport- och bilindustrin, genomgår en process som kallas "laminering". Denna behandling innebär att man monterar två eller flera glaspaneler och applicerar en eller flera plastfilmer mellan dem, som om de var en smörgås. Dessa skikt förenas genom att man applicerar värme och tryck för att bilda en stark, värmebeständig och dragprodukt, kan tillverkas i olika färger, erbjuder ljudisolering och kan användas som filter för ultraviolett solljus. Det finns tre huvudmetoder för bearbetning av laminerat glas.
Typer av laminering
Ett av de mest använda inre skikten är PVB - Polyvinylbutyralskiktet. Vanligtvis har den en tjocklek av 0,38 mm som kan förstoras till 0,76 mm för att bilda en mer resistent produkt, såsom till exempel vindrutan av bilrör.
EVA, etylen och vinylacetat används för inre lamineringsskiktet och ger slutprodukten större transparens, hållbarhet som gör den mer resistent mot höga och låga temperaturer. Tillsammans med EVA kan dekorativa material substrat placeras mellan panelerna för att skapa mönster och bilder inuti glaset.
PU, polyuretan och TPU, termoplastisk polyuretan, används också som innerskikt för laminerat glas. Den genomskinliga profilen som tillverkas med PU och TPU används i genomskinliga täcker av cockpits av flygplan, pansarbilar, dörrar till banker, kedjor och ambassader.
Autoklavmetod
Den traditionella metoden för glaslaminering använder autoklaven - en kammare som använder värme och tryck för att slutföra den permanenta bindningen mellan tre eller flera lager. För det första går glasskivorna till ett rent område för att de ska vara fria från fukt och smuts. De tas sedan till ett luftkonditioneringssystem med hjälp av trycklås. Varje glasplåt är rent och tar emot den inre filmen och ett annat glasplåt. Med en vakuumlamineringsmetod är glasskivans smörgås smält. Slutligen överförs materialet till autoklavmaskinen och utsätts för hög värme och tryck för att ansluta glasskikten och avlägsna resterande luftfickor.
Metod utan autoklav
För närvarande har glaslamineringsprocessen utförts med hjälp av en ny metod som inte använder autoklav. Detta system använder ugnar, kallade värmeugnar, istället för stora traditionella autoklaver, och kräver inte vakuumlamineringssteget. Först splittras glaset och rengörs. Därefter placeras skikten med PVB eller EVA mellan dem. Glasmassan går till uppvärmningsbord och all luft dras från den. Uppvärmningsugnen placeras på bordet och uppvärmningen börjar, vilket kan ta upp till 190 minuter, beroende på glasets tjocklek och typen av innerskikt som appliceras. Efter uppvärmning förväntas enheten svalna och sedan tas den bort från bordet.
Gjuten på plats
CIP-lamineringsprocessen eller Cast In Place uppnås genom att placera två glasstycken parallellt med varandra med mycket lite utrymme mellan dem och därefter hälls flytande harts i detta område. En typ av CIP-glas polymeriseras sedan genom katalys eller UV-strålning. Den andra, den kalla processen, kräver inte tryck, ljus eller värme. Denna process börjar när två glasstycken förseglas och ett aktiverat harts införes mellan skikten. Glasmixan placeras horisontellt för att avlägsna restluft. Sidorna är förseglade, glaset går igenom en läkningsprocess på 10 till 12 timmar. Typen av CIP-laminering används för tillverkning av laminerade glasskivor utanför standarddimensionerna.